Wind Turbine Aerodynamics: Understanding Blade Design Principles
Building a small-scale wind turbine is a rewarding project, blending engineering, science, and a desire for sustainable energy. While mechanical construction is crucial, the performance of your turbine largely hinges on its aerodynamic efficiency. This article delves into the essential principles of wind turbine blade design, helping you understand how to maximize energy capture.
The Role of Airfoil Shape
At the heart of efficient wind turbine blade design lies the airfoil. An airfoil is the cross-sectional shape of the blade, and it's carefully engineered to generate lift – the force that drives the turbine's rotation. Think of an airplane wing; the airfoil shape is what allows it to soar. Wind turbine blades operate on the same principle, but with critical differences to account for wind speed variability and rotational forces.
A classic airfoil shape is asymmetrical: the upper surface is more curved than the lower surface. As wind flows over the curved upper surface, it has to travel a longer distance, which means it speeds up. According to Bernoulli's principle, faster-moving air exerts less pressure. Conversely, the slower-moving air under the blade creates higher pressure. This pressure difference – the lift – pushes the blade upwards and drives the turbine.
Numerous airfoil designs exist, each with strengths and weaknesses. The choice of airfoil depends on the desired characteristics, such as maximum power output, starting torque (ability to start rotating in light winds), and noise reduction. For small-scale turbines, simpler, readily available airfoil profiles often suffice. Understanding the basics of lift coefficient (Cl) and drag coefficient (Cd) is key to evaluating different airfoils. A higher Cl and lower Cd are generally desirable.
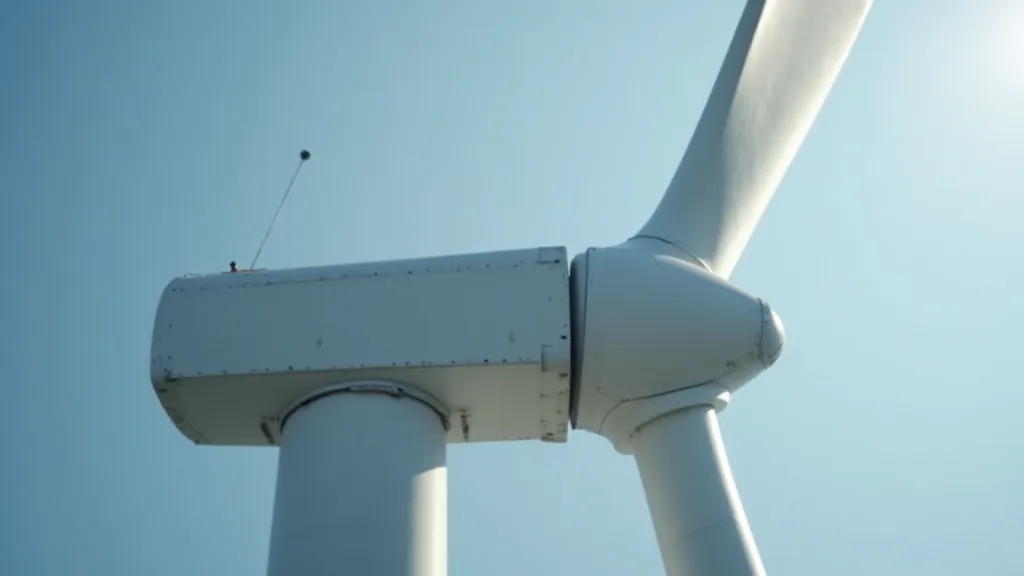
The Importance of Pitch Angle
The pitch angle is the angle between the blade’s chord line (an imaginary line from the leading edge to the trailing edge) and the direction of the incoming wind. It's a critical parameter for controlling the turbine’s performance and preventing damage.
Increasing the pitch angle generally increases the lift force, but it also increases the drag. Finding the optimal pitch angle is a balance – maximizing lift while minimizing drag. The ideal pitch angle varies with wind speed. In low wind conditions, a higher pitch angle can help the turbine start rotating. In higher winds, a lower pitch angle is needed to prevent the turbine from overspeeding and potentially damaging itself.
Fixed-pitch turbines have a constant pitch angle, while variable-pitch turbines (more common in large commercial turbines) can adjust the pitch angle dynamically based on wind speed. The materials used in blade construction are equally important; choosing the right material significantly impacts performance and durability. If you're exploring different options, you might find our comparison of choosing the right wind turbine blade material – including PVC, wood, and fiberglass – to be insightful.
Blade Twist and Taper
Real-world wind turbine blades aren’t perfectly straight. They incorporate blade twist. This means the pitch angle changes along the blade's length. This is necessary because the relative wind speed experienced by different parts of the blade differs as the blade rotates. The tip of the blade travels faster than the root (the part closest to the hub).
Blade taper, which refers to the blade's width decreasing from root to tip, is another common design feature. Tapering helps to distribute the aerodynamic loads more evenly along the blade, reducing stress and improving overall efficiency. The combination of twist and taper requires careful consideration, as they interact to influence the turbine's overall efficiency. The choice of materials, of course, plays a vital role too, especially when dealing with the stresses created by these design features.
Understanding Solidity and Blade Number
Solidity refers to the total area of the blades divided by the area swept by the rotor. A higher solidity generally means more torque, which is useful for starting in low winds, but it also increases drag. A lower solidity provides less torque but more speed.
The number of blades also influences performance. Most small-scale turbines have between 2 and 5 blades. Fewer blades result in higher tip speeds and potentially higher power output, but they also create more turbulence. More blades create more starting torque. It's a balancing act, as each design choice impacts the turbine’s overall performance characteristics, and the right choice will depend on your specific goals. Before embarking on your project, you might appreciate considering the broader context of scaling your turbine; our article on sizing your wind turbine offers valuable insights.
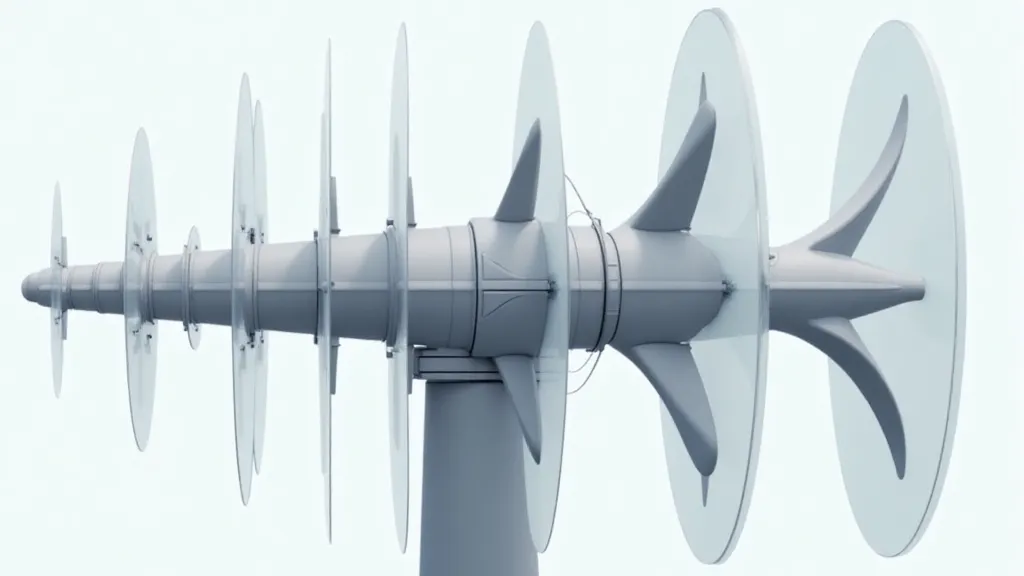
Materials and Structural Considerations
While this article focuses on aerodynamics, it's crucial to remember that the blades must also be structurally sound. The chosen material must be strong enough to withstand the bending forces generated by the wind and lightweight to minimize rotational inertia. Common materials for small-scale wind turbine blades include wood, PVC, fiberglass, and carbon fiber. Each material offers a unique set of advantages and disadvantages in terms of strength, weight, cost, and ease of fabrication.
Wood is readily available and easy to work with, but it can be susceptible to moisture and rot. PVC is lightweight and inexpensive, but it's not as strong as other materials. Fiberglass offers a good balance of strength and weight, while carbon fiber is the strongest and lightest option, but it's also the most expensive and difficult to work with. The ideal choice will depend on your budget, skill level, and the specific requirements of your project. Understanding these material properties is fundamental to creating a durable and efficient wind turbine.
Beyond the material itself, the construction techniques you employ significantly influence the blade's structural integrity. Careful attention to detail, including proper bonding and reinforcement, is essential for preventing premature failure. It's also worthwhile to explore various blade profiles and airfoil shapes, as these can dramatically impact aerodynamic performance. Ultimately, the success of your wind turbine project will depend on a combination of sound engineering principles, careful material selection, and meticulous craftsmanship.

Advanced Considerations: Dynamic Pitch and Active Control
For more advanced designs, especially those aiming for higher efficiency and broader operating ranges, dynamic pitch control and active control systems become increasingly relevant. Dynamic pitch control involves continuously adjusting the blade's pitch angle based on real-time wind conditions, optimizing power output and reducing loads on the turbine. Active control systems take this a step further, incorporating sensors and sophisticated algorithms to fine-tune the turbine's operation, maximizing efficiency and minimizing downtime. While these technologies add complexity and cost to the project, they can significantly improve overall performance and reliability.
Conclusion
By understanding these aerodynamic principles, you can make informed decisions about blade design and construction, ultimately leading to a more efficient and reliable small-scale wind turbine. Whether you're a student tackling a science project or a hobbyist looking to harness renewable energy, a solid understanding of wind turbine aerodynamics is key to success.